

Testing & Analysis
Testing



Testing Process
We tested the KnitFix on various clothing items such as jeans and shirts to determine if the stitch would stay secure. We found that the stitch was very comfortable and stayed attached to the material even after we put it through the wash. The user can easily walk, sit, and go about their day without worrying that the stitch will fall off.
The internal mechanisms were also tested thoroughly, and we found that the hooking, threading, crimping, and cutting mechanisms all worked successfully independently. We tested each process by prototyping them on a larger scale and then making them to size. We sized the mouth of the KnitFix accordingly to fit various materials, including jeans, shirts, sweaters, and other fabrics. Then, we tested the needle sharpness on these different fabrics to ensure it would easily pierce them so the needle could thread through.
Analysis
We conducted Finite Element Analysis on the needle and pliers to understand the necessary length of the needle and to ensure the needle and pliers wouldn't break when force was applied.
Needle Length

When considering how to ensure that our needle is strong enough to withstand use on thicker fabrics like jeans, we first decided to analyze its strength based on the beam buckling equation:
​
​
​
Using Newton's second law, F=m*a, we determined the force required to pierce the jeans is 35N. We then rearranged the buckling equation to find the necessary needle length:
​
​
Using the equation for moment of inertia for a rectangular cross section, which is the cross section of the first part of the needle:
​
​
We found that the moment of inertia was 3.125 x 10 m. The elastic modulus for the steel needle is 200 gpa. Using these equations, we were able to determine that the critical needle length for buckling was 42.519mm. With our original needle design, which was 60mm, we found that the needle length was too long.
In order to make up for this design flaw, we created supports along the track less than 43mm apart, the largest of which being 18.5mm. This helps to maintain the safety and integrity of the needle over multiple uses.
​

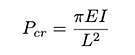

14
2
Needle Tip
The tip of the needle is unlike a normal needle as the eye of the needle is at the front. This results in a region of very little material at the front of the needle which has the potential to experience a large amount of force. In order to determine whether the design of the needle would withstand forces up to 35N, finite element analysis was performed on the needle tip. The needle was cut to be the size that extrudes outside of the pusher.

Finite Element Analysis was performed on the needle tip. The simulation was run 12 times to ensure convergence occurred. After each iteration, the mesh was refined. The convergence of the Maximum Von Mises Stress is seen in the figure above.


The minimum factor of safety was found to be 15. Since stainless steel is a ductile material, this factor of safety is very high. Such a high factor of safety ensures that the needle will not break, even if a much larger force that 35N is applied.
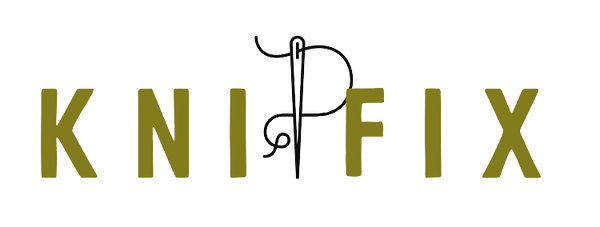

Pliers
The pliers are a very complex shape with small geometries. To ensure that the pliers do not break during operation, finite element analysis was performed on each plier part.
​
Moving piece:
​



The minimum factor of safety was found to be 2.695. Since stainless steel is a ductile material, this factor of safety is lower than ideal as ideally, the factor of safety for ductile failure should be above 3. The minimum factor of safety emerges in the thin geometry part that attaches the base of the crimper to the plier arm. To improve the structural integrity in the future, we would increase the thickness of this part.
​
Stationary piece:
​

The minimum factor of safety was found to be 110. Since stainless steel is a ductile material, this factor of safety is very high. The KnitFix Group has sees no need for any future improvement to the stationary plier piece as analysis shows it will withstand the force without any failure.

